Thermisches Spritzen: Präzise Oberflächenveredelung
Die DURMAT®-Produktpalette bietet für folgende Thermische Spritzverfahren qualitativ hochwertige Werkstoffe an:
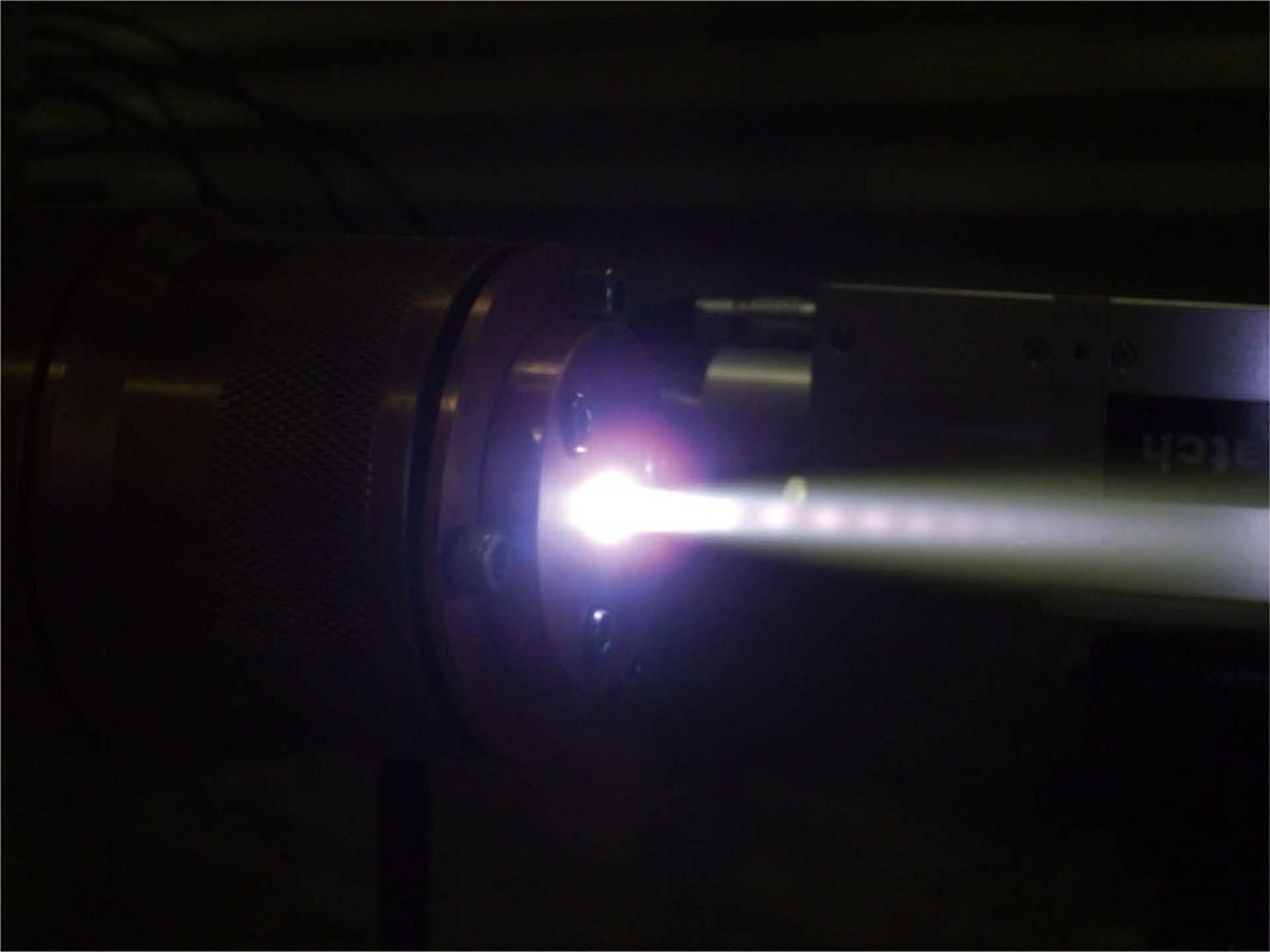
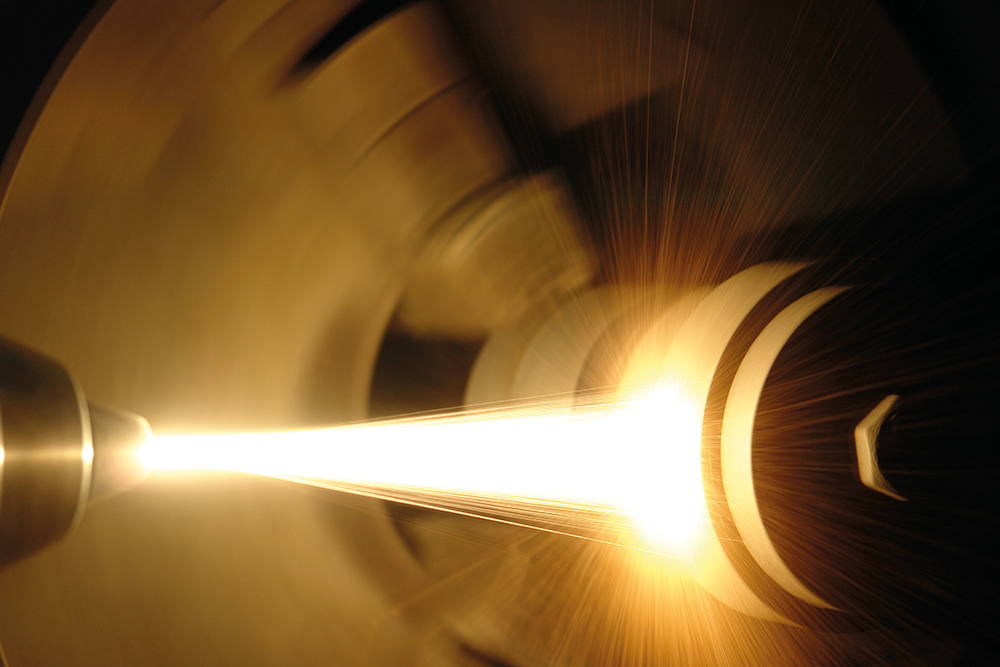
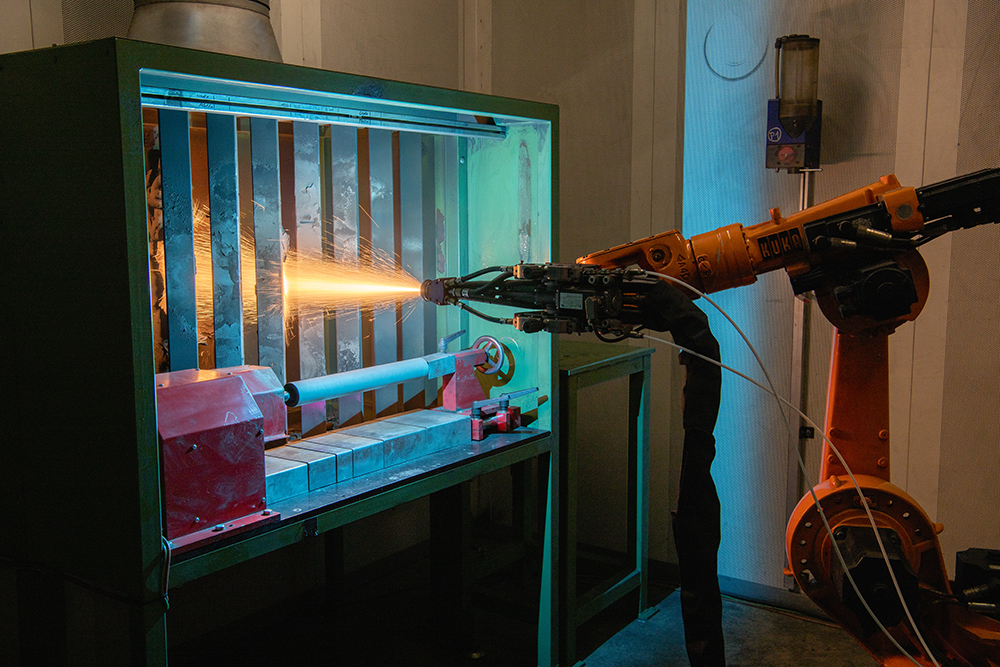
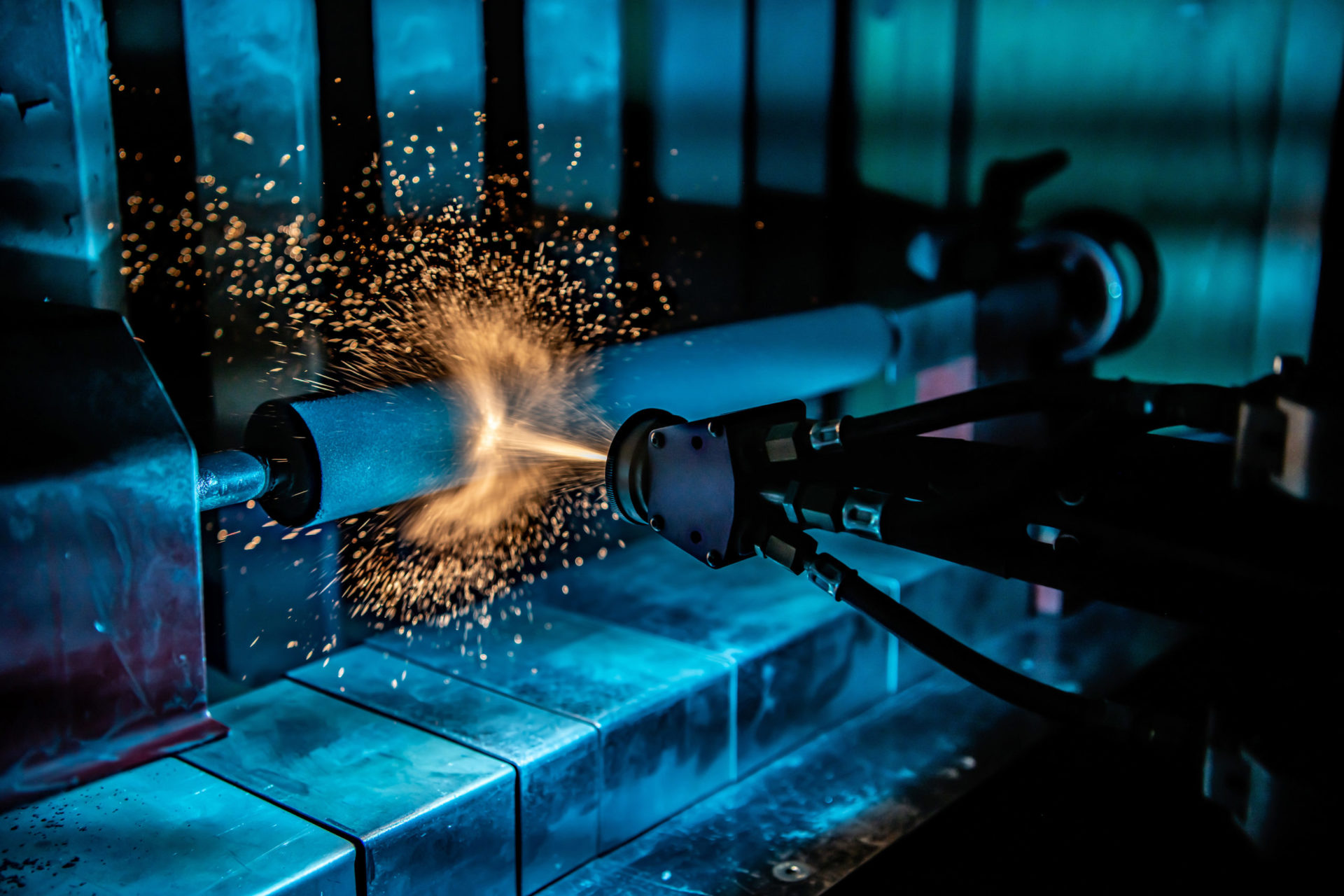
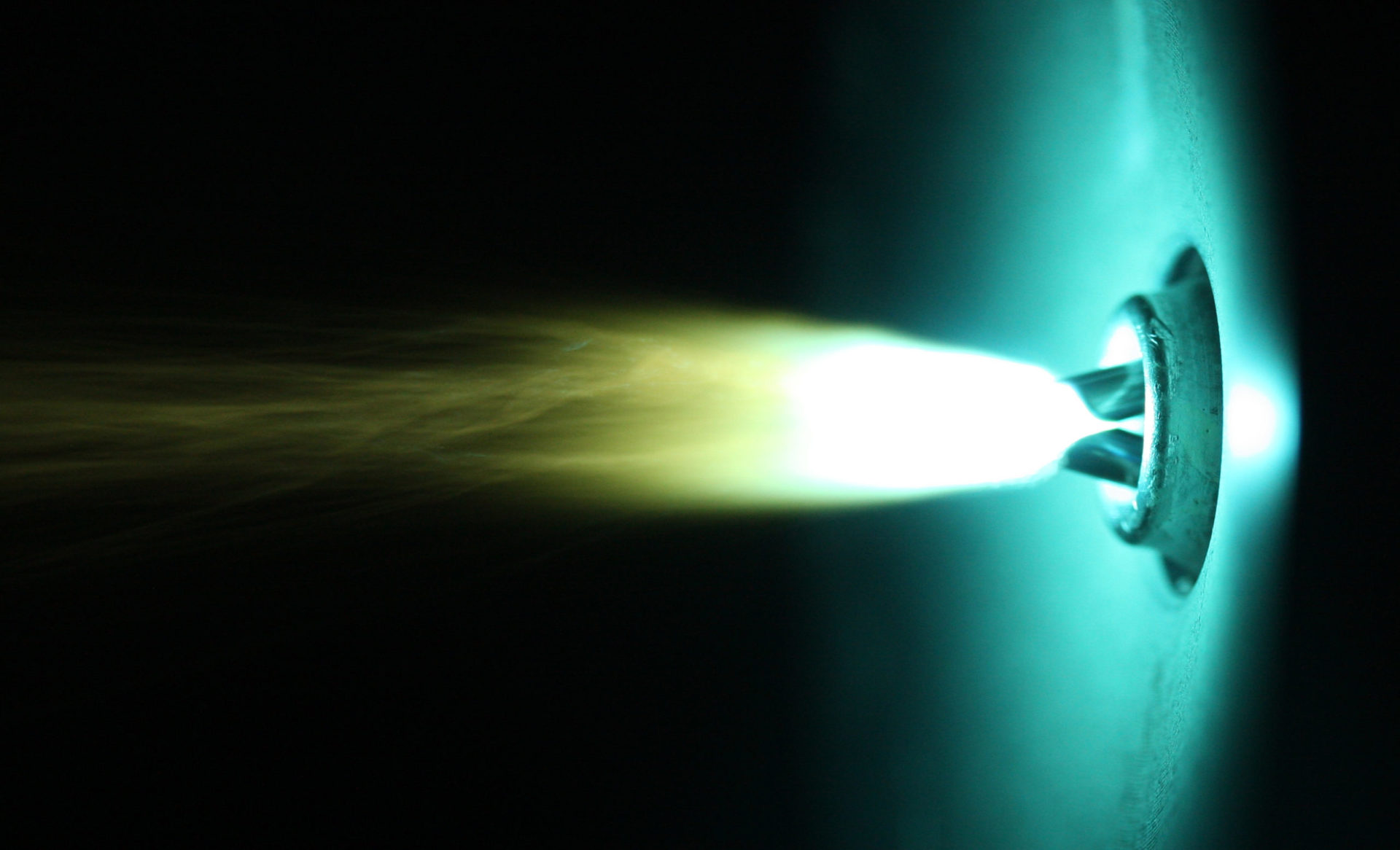
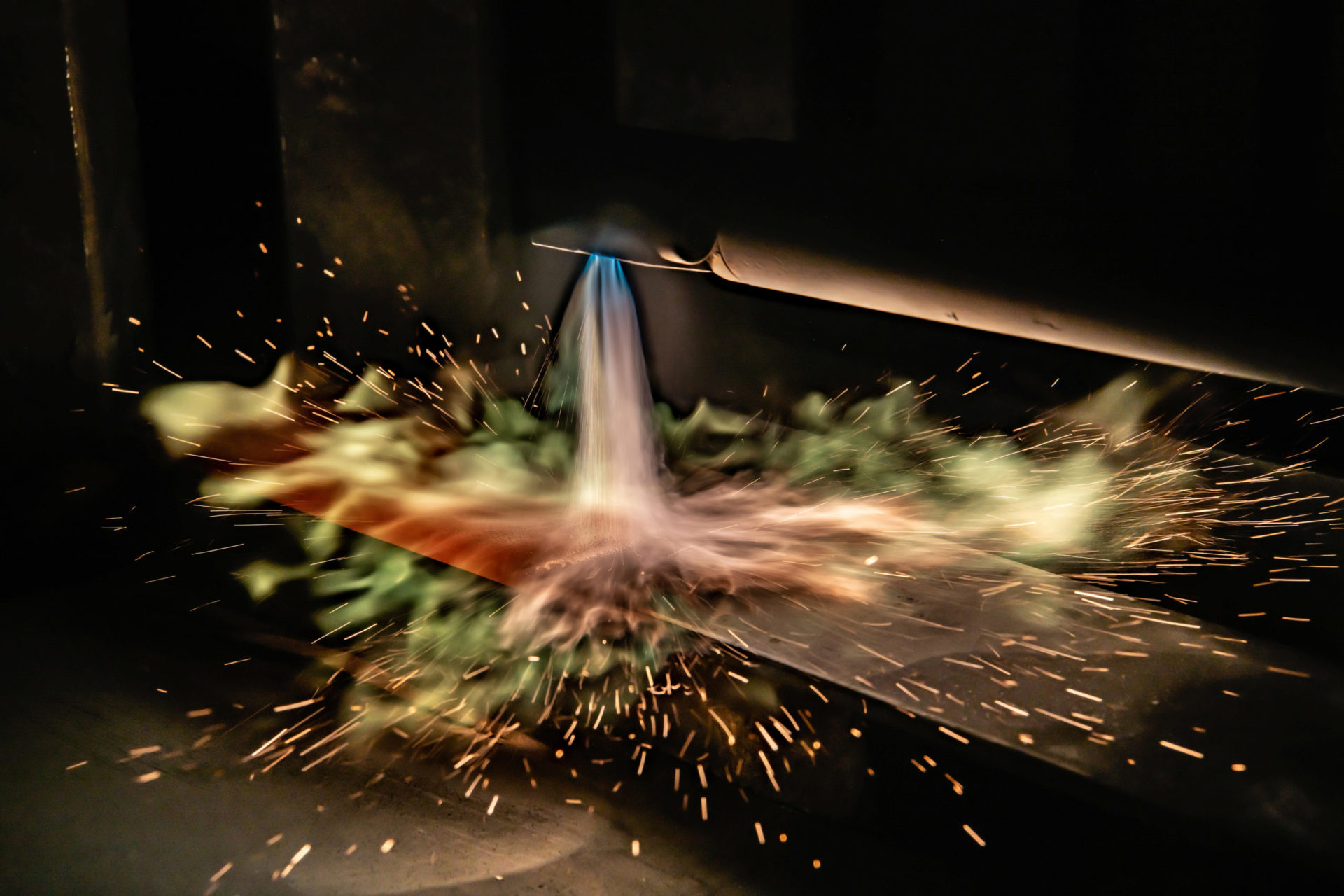
Rückruf Service
Thermische Spritzverfahren
Lichtbogendrahtspritzen (Libo)
Das Lichtbogenspritzen zeichnet sich vor allem durch hohe Auftragsraten von bis zu 80 kg/h und möglicher Herstellung von Schichtdicken bis zu mehreren Millimetern sowie einer sehr robusten Technik mit gleichzeitig leichter Handhabung aus. Deshalb wird das Spritzverfahren oftmals auch mobil auf Baustellen angewendet. Ein ausschlaggebender Vorteil des Lichtbogenspritzens ist die Tatsache, dass keine brennbaren Prozessgase erforderlich sind, womit das Verfahren an Sicherheit gewinnt und eine gute Energieausnutzung erzielt. Als Haupteinsatzgebiet gilt der Korrosions- und Verschleißschutz.
Funktionsweise des Lichtbogendrahtspritzens
Pulverflammspritzen
Beim Pulverflammspritzen wird der pulverförmige Zusatzwerkstoff im Düsensystem der Spritzpistole mit einer Acetylen-Sauerstoff-Flamme (thermische Energie) an- oder aufgeschmolzen und mit entsprechender Geschwindigkeit (kinetische Energie) auf die vorgesehenen Werkstückbereiche aufgebracht. Falls erforderlich, kann zur Beschleunigung der Pulverteilchen auch noch ein zusätzliches Gas (z. B. Argon oder Stickstoff) verwendet werden. Die Vielfalt der Spritzzusatzwerkstoffe ist bei den Pulvern mit weit über 100 Materialien sehr weit gefächert.
Bei den Pulvern unterscheidet man selbstfließende und selbsthaftende Pulver. Die selbstfließenden Pulver benötigen meist zusätzlich eine thermische Nachbehandlung. Dieses „Einschmelzen“ erfolgt überwiegend mit den dafür hervorragend geeigneten Acetylen-Sauerstoff-Brennern.
Durch den thermischen Prozess wird die Haftung von Spritzschicht auf dem Grundwerkstoff erheblich gesteigert; die Spritzschicht wird gas- und flüssigkeitsdicht.
Drahtflammspritzen
Beim Drahtflammspritzen wird der pulverförmige Zusatzwerkstoff im Düsensystem der Spritzpistole mit einer Acetylen-Sauerstoff-Flamme (thermische Energie) an- oder aufgeschmolzen und mit entsprechender Geschwindigkeit (kinetische Energie) auf die vorgesehenen Werkstückbereiche aufgebracht. Falls erforderlich, kann zur Beschleunigung der Pulverteilchen auch noch ein zusätzliches Gas (z.B. Argon oder Stickstoff) verwendet werden. Die Vielfalt der Spritzzusatzwerkstoffe ist bei den Pulvern mit weit über 100 Materialien sehr weit gefächert.
Bei den Pulvern unterscheidet man selbstfließende und selbsthaftende Pulver. Die selbstfließenden Pulver benötigen meist zusätzlich eine thermische Nachbehandlung. Dieses „Einschmelzen“ erfolgt überwiegend mit den dafür hervorragend geeigneten Acetylen-Sauerstoff-Brennern.
Durch den thermischen Prozess wird die Haftung von Spritzschicht auf dem Grundwerkstoff erheblich gesteigert; die Spritzschicht wird gas- und flüssigkeitsdicht.
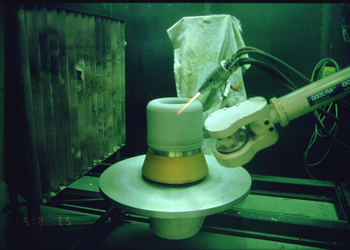
Hochgeschwindigkeitsflammspritzen (HVOF / HVAF)
Das Hochgeschwindigkeitsflammspritzen (HVOF, abgeleitet von High-Velocity-Oxygen-Fuel) ist ein thermisches Beschichtungsverfahren zur Oberflächenbearbeitung. Beim Hochgeschwindigkeitsflammspritzen erfolgt eine kontinuierliche Kraftstoffverbrennung unter hohem Druck innerhalb einer wasser- oder luftgekühlten Brennkammer. Als Kraftstoffe werden Brenngase (wie z. B. Propan, Ethylen, Propen, Butan, Acetylen, Wasserstoff), flüssige Brennstoffe (z. B. Diesel, Kerosin) sowie auch Kombinationen von diesen eingesetzt. Das Oxidationsmittel ist meistens Sauerstoff, aber auch Luft (gebräuchliche Verfahrensbezeichnung: HVAF, abgeleitet von High-Velocity-Air-Fuel). Der in der Brennkammer erzeugte hohe Druck des brennenden Kraftstoff-Sauerstoff-Gemisches und die (meist nachgeordnete) Expansionsdüse (Lavaldüse) erzeugen die notwendige hohe Geschwindigkeit des Gasstrahls.
Meistens pulverförmige Spritzwerkstoffe (Korngröße 1–150 µm), aber auch als Stäbe und Drähte verfügbar, werden axial in der Brennkammer oder radial im Bereich der Expansionsdüse zugeführt. Dadurch werden die Spritzpartikel auf die hohen Geschwindigkeiten beschleunigt, die zu sehr dichten Spritzschichten mit hervorragenden Hafteigenschaften führen. Durch die regelbare und gerade ausreichende Wärmeeinbringung wird der Spritzwerkstoff durch den Spritzprozess nur gering metallurgisch verändert.
Einsatzgebiete sind: Kraftwerke, Luftfahrt-, Auto-, Papier- und Maschinenbau-Industrie.
Plasmaspritzen
Beim Atmosphärischen Plasmaspritzen (APS) sind in einem Plasmabrenner eine Anode und bis zu drei Kathoden durch einen schmalen Spalt getrennt. Durch eine Gleichspannung wird ein Lichtbogen zwischen Anode und Kathode erzeugt. Das durch den Plasmabrenner strömende Gas oder Gasgemisch wird durch den Lichtbogen geleitet und hierbei ionisiert. Die Dissoziation, beziehungsweise anschließende Ionisation, erzeugt ein hochaufgeheiztes (bis 20000 K), elektrisch leitendes Gas aus positiven Ionen und Elektronen.
In diesem erzeugten Plasmajet wird Pulver (übliche Kornverteilung: 5–120 µm, bei bestimmten Geräten ist auch eine Körnung von bis hinunter zu 100 nm möglich) eingedüst, das durch die hohe Plasmatemperatur aufgeschmolzen wird. Der Plasmastrom reißt die Pulverteilchen mit und schleudert sie auf das zu beschichtende Werkstück/Bauteil/Substrat. Die Gasmoleküle kehren bereits nach kürzester Zeit wieder in einen stabilen Zustand zurück und so sinkt die Plasmatemperatur bereits nach kurzer Wegstrecke wieder ab.
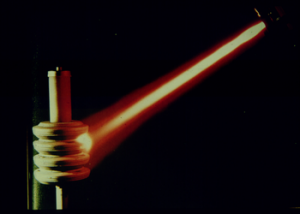
Anbringung der Plasmabeschichtung und weiteres Vorgehen
Die Plasmabeschichtung erfolgt in normaler Atmosphäre, inerter Atmosphäre (unter Schutzgas wie Argon), in Vakuum oder auch unter Wasser. Für die Schichtqualität sind die Geschwindigkeit, Temperatur sowie die Zusammensetzung des Plasmagases von Bedeutung. Besondere Abwandlungen wie das PTWA (PTWA-Verfahren für Plasma Transferred Wire Arc) verwenden anstatt des Pulvers einen Draht, was zu einem einfacheren Aufbau des Brenners führt. Plasmaspritzen unter Vakuum wird als VPS bezeichnet.
Beim Schutzgas-Plasmaspritzen wird der gesamte Vorgang mit Schutzgas (meist Stickstoff) als Transportgas durchgeführt. Vorteil hierbei ist die sehr geringe Oxidation der Partikel zwischen Brenner und Substrat.
Verwendete Gase sind Argon, Stickstoff, Wasserstoff, Helium oder Kombinationen daraus. Durch die sehr unterschiedlichen Prozessparameter können eine Vielzahl von Beschichtungen realisiert werden, sodass es nahezu in jeder Branche Anwendungsfelder gibt. Wichtige Industriezweige, in denen Plasmaspritzen eingesetzt werden, sind die Automobilindustrie, die Papier- und Druckindustrie, die Luft- und Raumfahrtindustrie, die Abfallindustrie und die energieerzeugende Industrie.
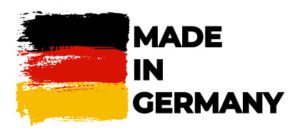