2024 - We are celebrating our 40th anniversary!
DURUM's wear-resistant materials are in demand worldwide - and are used in a wide variety of industries. With the development of DURMAT® NIFD® and DURMAT® NISE®for which DURUM has also been granted a patent, we have also set a milestone in the development of DURUM wear protection.
Often copied and never equaled. Many of our competitors have tried to copy DURMAT® NIFD® over the years. We see it as praise and recognition that we have developed something special.
We don't want to rest on our laurels. A little more than 30 years after the DURMAT® NIFD® The next innovative step follows with the granting of the patent, almost to celebrate our 40th anniversary: DURMAT® NIFD® ON
A seamless cored wire with exceptional welding properties and partially increased tungsten content. DURUM: Progress through research and development.
Seamless cored wires for wear protection are special welding consumables that are used for hardfacing and repairing surfaces subject to wear. In contrast to closed-form cored wires, seamless cored wires consist of a continuous metal sheath without a seam that encloses the powder inside.
The advantages of seamless cored wires lie in their structural properties. Due to the special design, the cored wire has a uniform powder filling and a constant wire geometry. This protects it from deformation stresses and makes it suitable for feeding over long distances - DURMAT® NIFD® ON is particularly suitable for automated welding processes and has good conveyability in welding systems.
DURMAT® NIFD® ON has a high proportion of fused tungsten carbide (WSC) in a self-flowing nickel matrix. The cored wire is composed of approx. 60% WSC and 35-40% matrix. This alloy has a low melting interval and self-flowing properties, resulting in a smooth and clean surface. The matrix is also resistant to acids, bases, alkalis and other corrosive media.
We have developed our seamless cored wire especially for semi-automatic and fully automatic robot welding. Typical applications are repair and hardfacing of ferritic and austenitic steel tools and machine parts. The product is used in the oil and gas industry, in mining, for oil press parts, transport screws, cellulose mixing blades, mill hammers and much more.
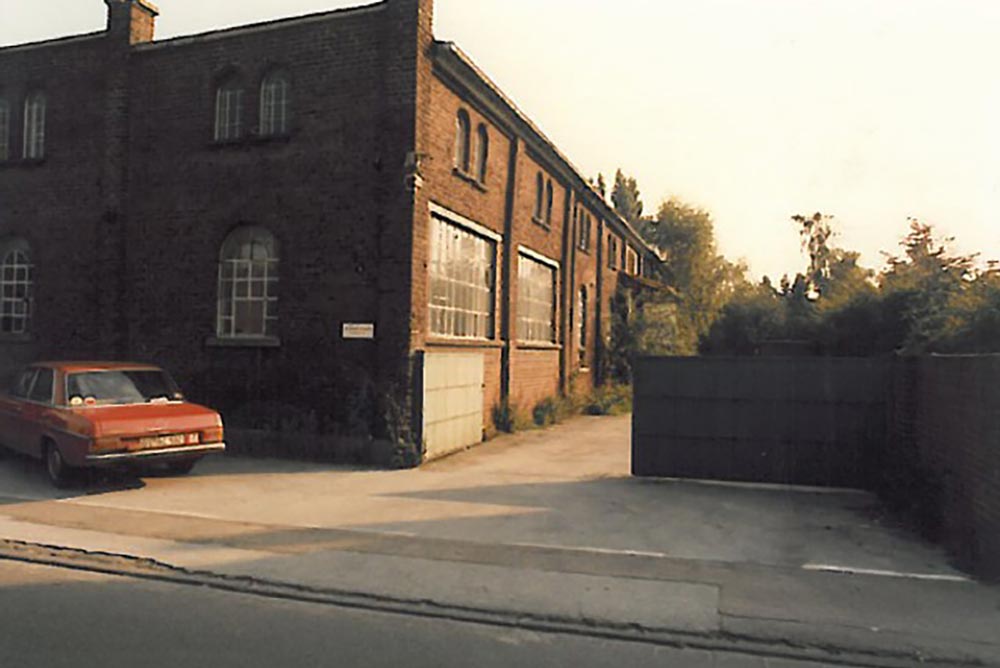
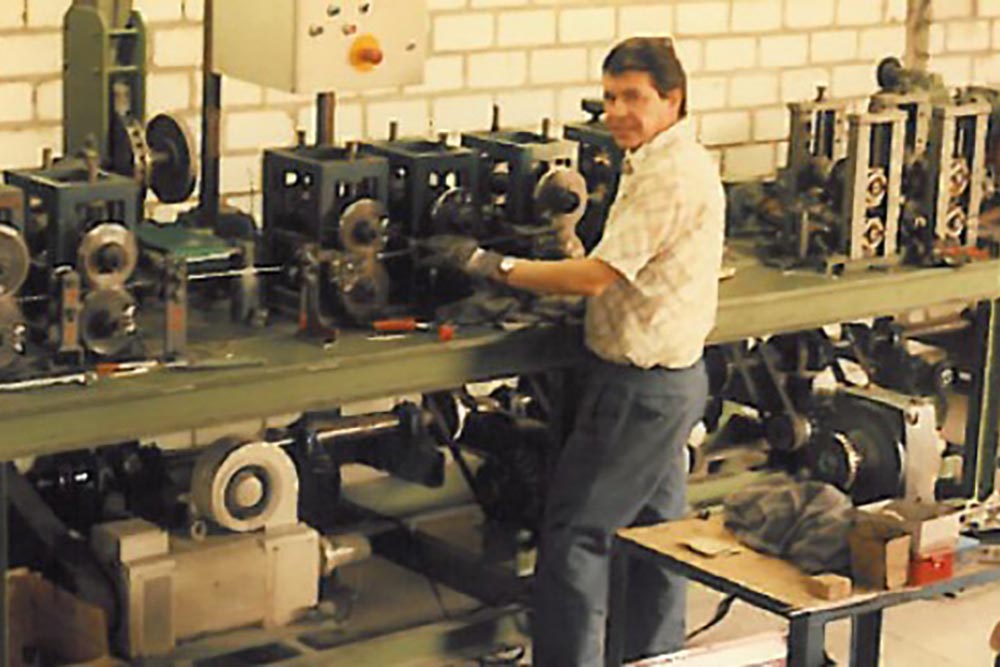
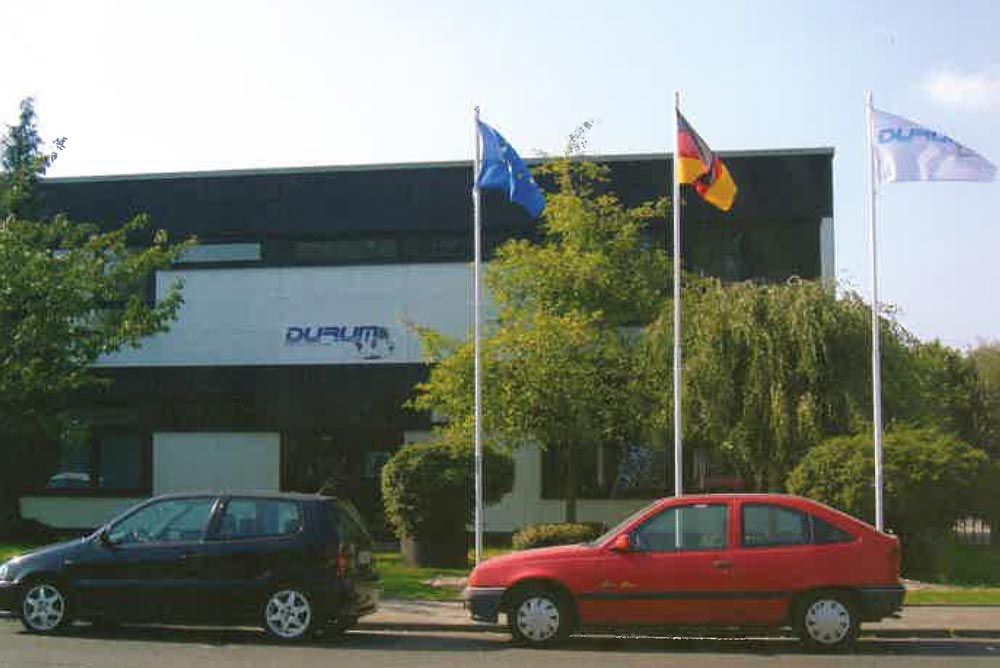
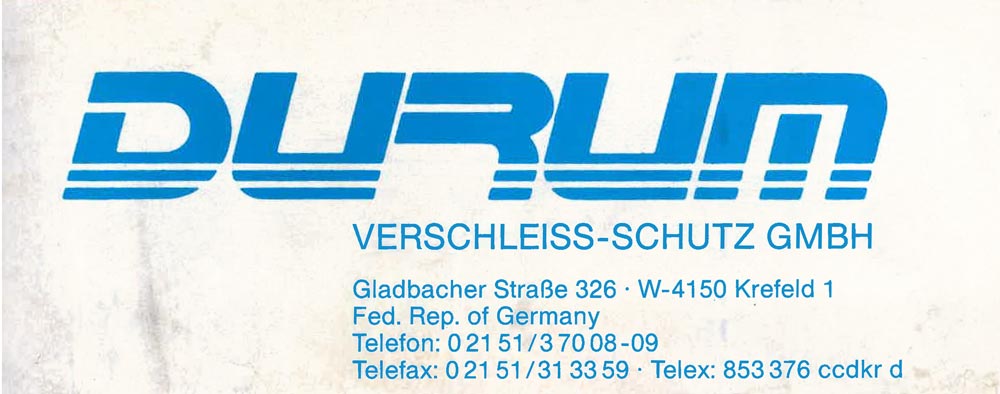

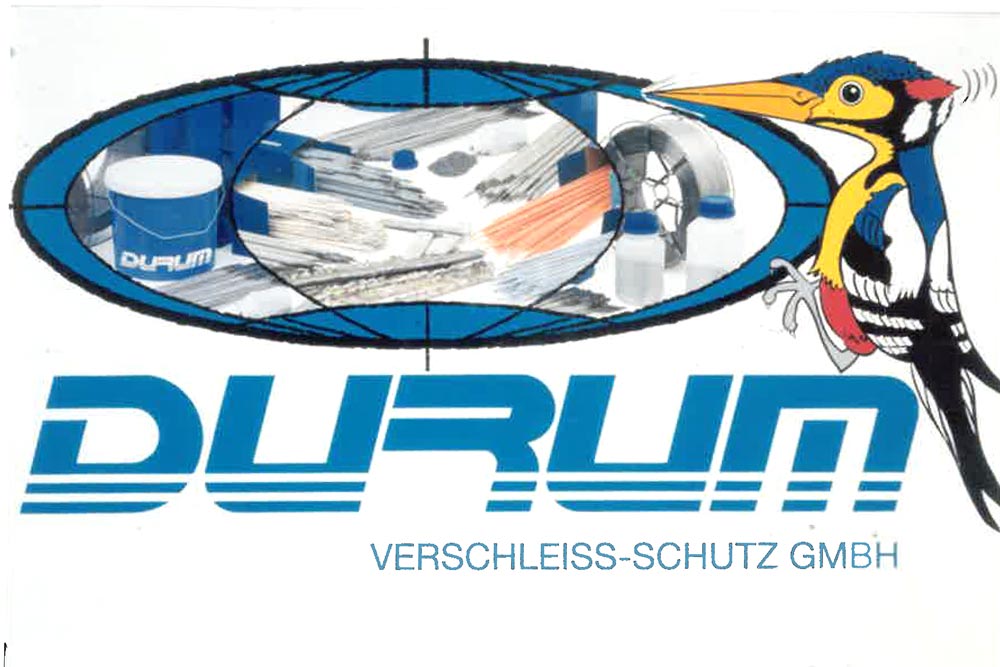
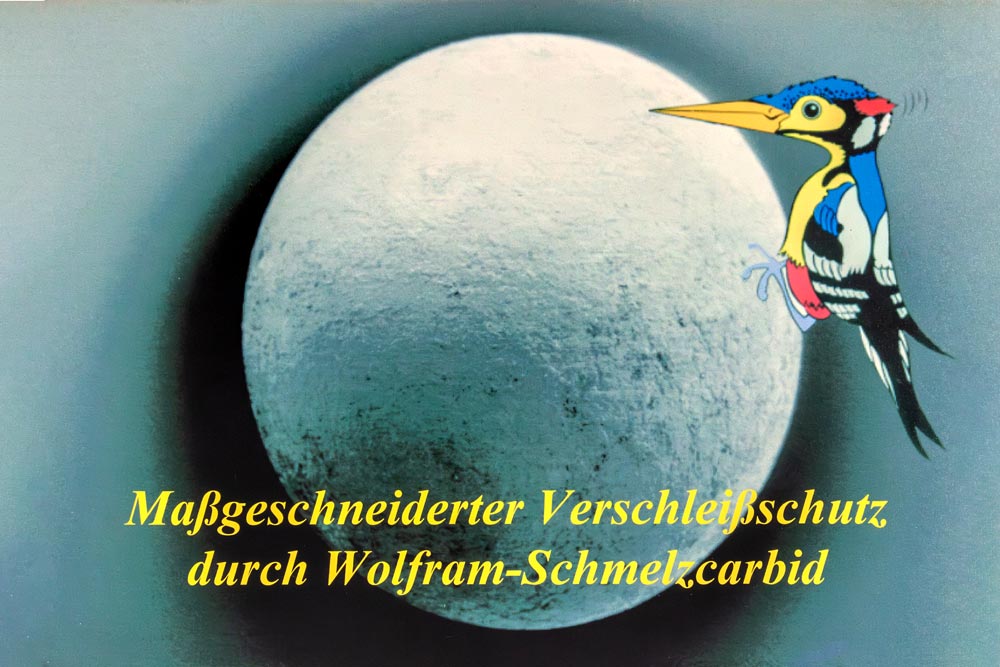
Certifications: DURUM offers tested quality
Our quality management has been certified in accordance with DIN EN ISO 9001 since 2015. In 2017, we also achieved certification as a welding company in accordance with DIN EN ISO 3834-2.
The Fearnley Group has developed its own certifications for quality and competence in the oil and gas industry. The requirements for process level certification have their own standards, which supplement the basic API and ISO standards with additional specifications.
What porcini mushrooms and Drafi Deutscher have to do with DURUM
"The history of DURUM begins with a portion of porcini mushrooms in a small tavern on Lake Garda. Since then, we have realized many exciting projects, created innovations and celebrated successes in 40 years of company history. True to the motto: marble, stone and iron break, but our protective layer does not." Peter Knauf, founder and managing director of DURUM Verschleiß-Schutz GmbH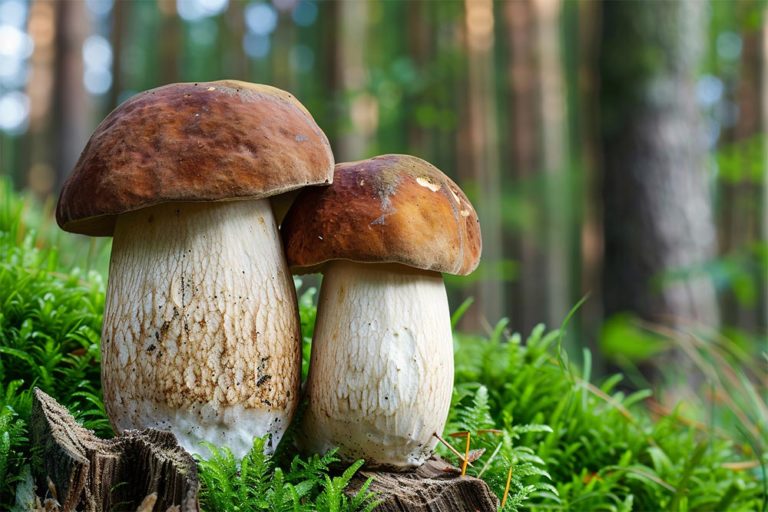
Our milestones
July 2014 to December 2016: Cooperation project with the Niederrhein University of Applied Sciences
The collaboration came about as part of the Central Innovation Program for SMEs (ZIM) of the Federal Ministry of Economics and Technology (BMWi). Together with the Niederrhein University of Applied Sciences in Krefeld, we developed a technology that can be used instead of laser cladding. Both the process technology, known as laser-like PTA deposition welding (LLP), and the plasma powder material were developed. As part of the project, the students had the opportunity to get to know the business world and gain practical experience. DURUM's task was to test and optimize the basic principles developed by the university for alloy development and the modification of welding torches under real conditions. The technology used in the project is cheaper than laser deposition welding while maintaining the same quality.
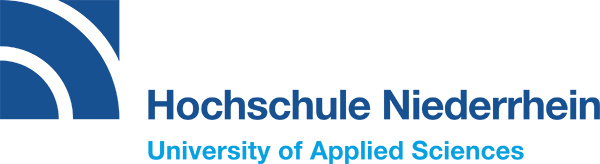
2003 - Salvage of the car freighter Tricolor

The car freighter Tricolor, loaded with new cars and on its way to the USA, sank in December 2002 after a collision in the English Channel. 30 kilometers off the French coast, the freighter, which weighed over 20,000 tons including its cargo, had to be sawn into nine pieces. Similar to the salvage of the Kursk, a wire saw from DURUM was used here. However, the requirements were different this time, as the dimensions of the car freighter presented a particular challenge. Due to the many car decks and nesting, many saw cuts had to be made. At the same time, the materials to be sawn were different for each cut. The saw therefore had to be designed differently to the Kursk. Depending on the section to be sawn, the saw chain had a length of 60 to 100 meters and a weight of 7 tons. The salvage of the Tricolor began in February 2003 and was completed in October 2004.
2001 - Sawing up the Kursk: salvage of a nuclear submarine
In August 2000, the Russian nuclear submarine Kursk sank after an explosion in the Barents Sea. Eight months later, work began to salvage the wreck. This was a dangerous operation, as there were still several live torpedoes in the partially destroyed bow. For this reason, the wreck first had to be cut open in order to salvage the rest of the submarine. DURUM produced a wire saw for this purpose, which was used to cut the bow from the rest of the ship underwater with the help of a robot. The wire saw was made from sleeves coated with JG-DUR carbide. After cutting it off, the wreck was successfully salvaged, while the bow with the torpedo section remained on the seabed.
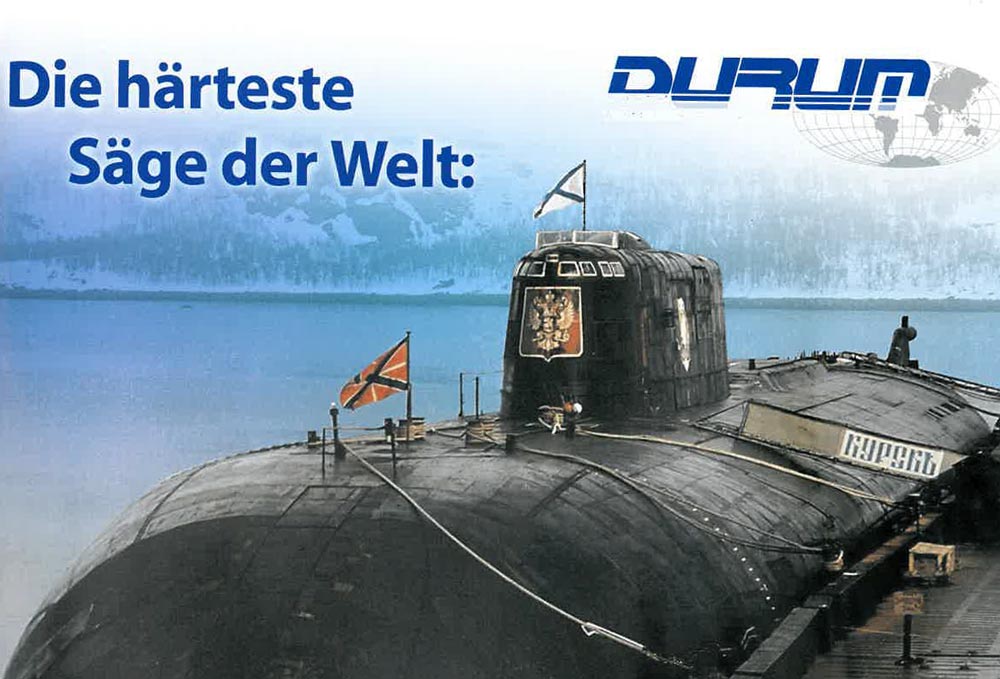
March 14, 1990 - First patent granted for DURMAT® NIFD
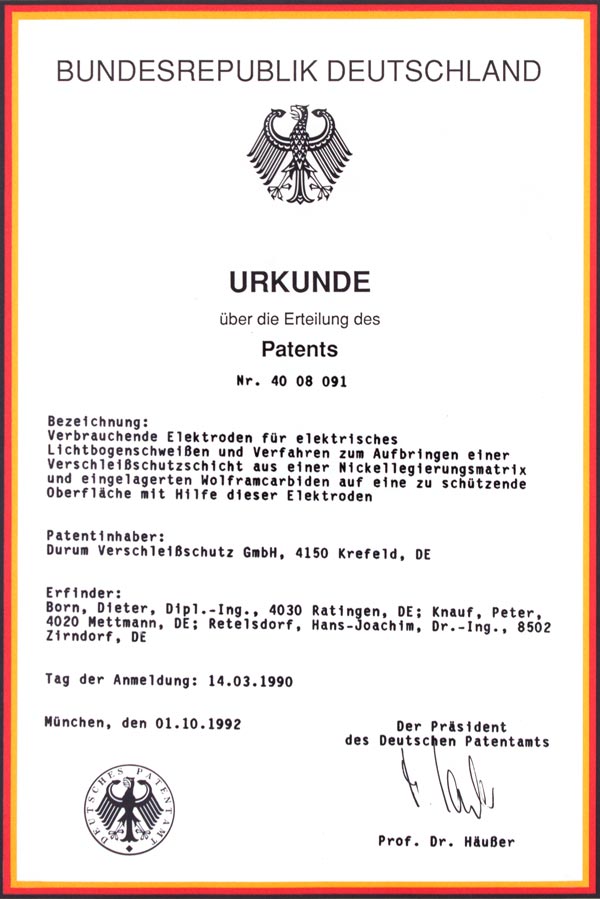
We first registered our patent in Germany and, over the years, also in the UK and the USA. Since DURUM launched this cored wire on the market, many material developers have tried to copy the product. To date, however, none of them have succeeded. DURMAT® cored wires are unique.