Deposition welding: fusing properties
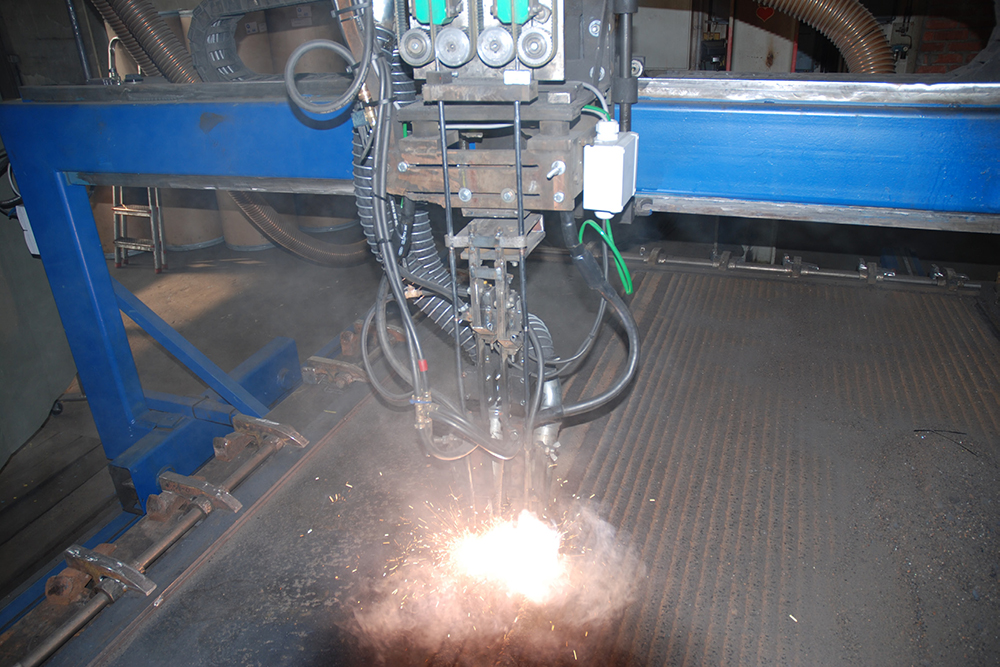
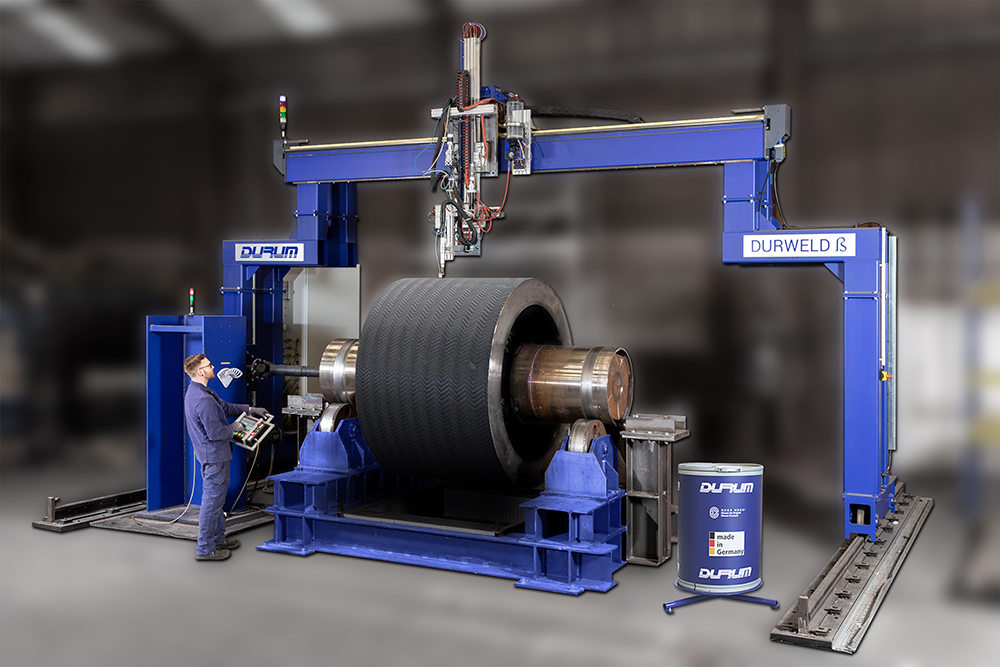
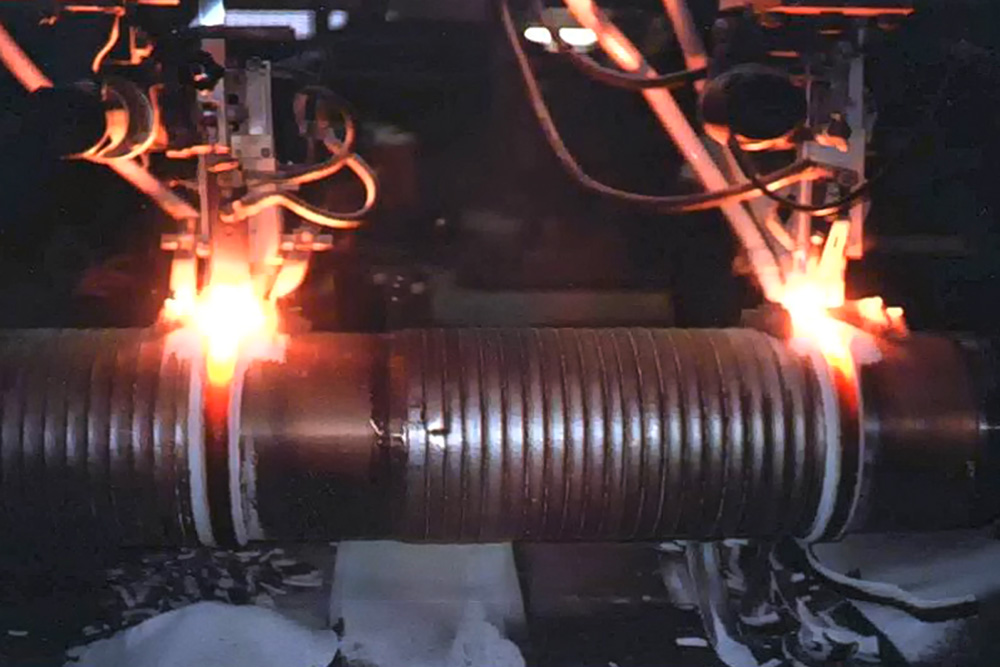
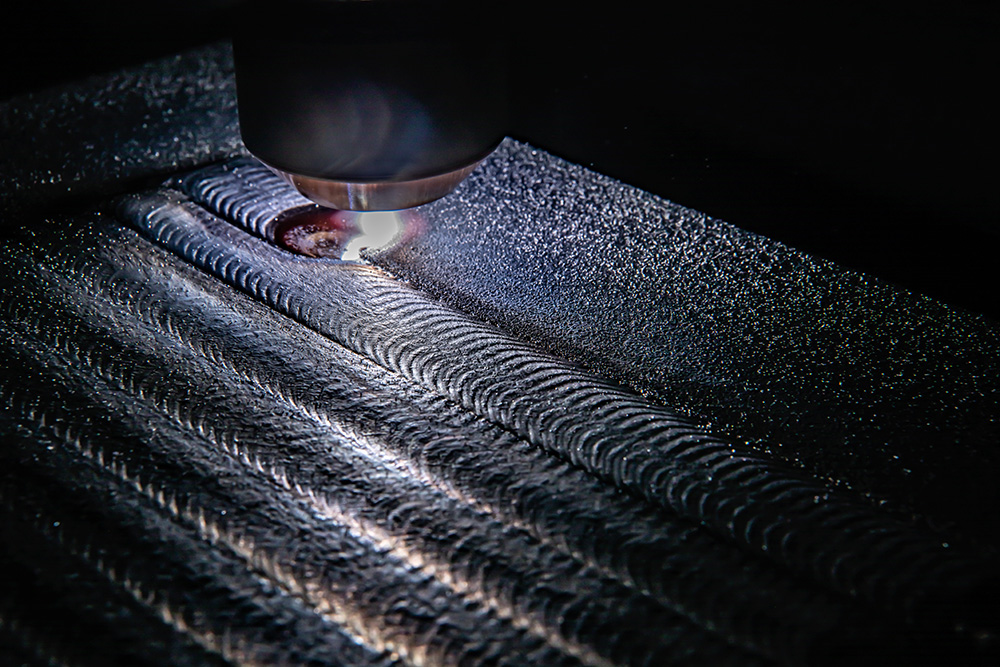
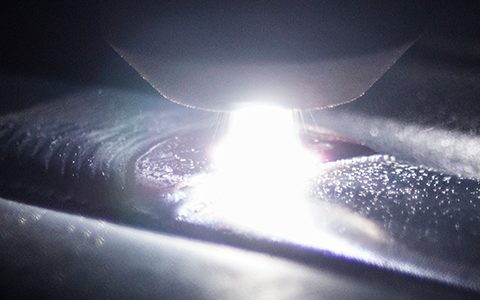
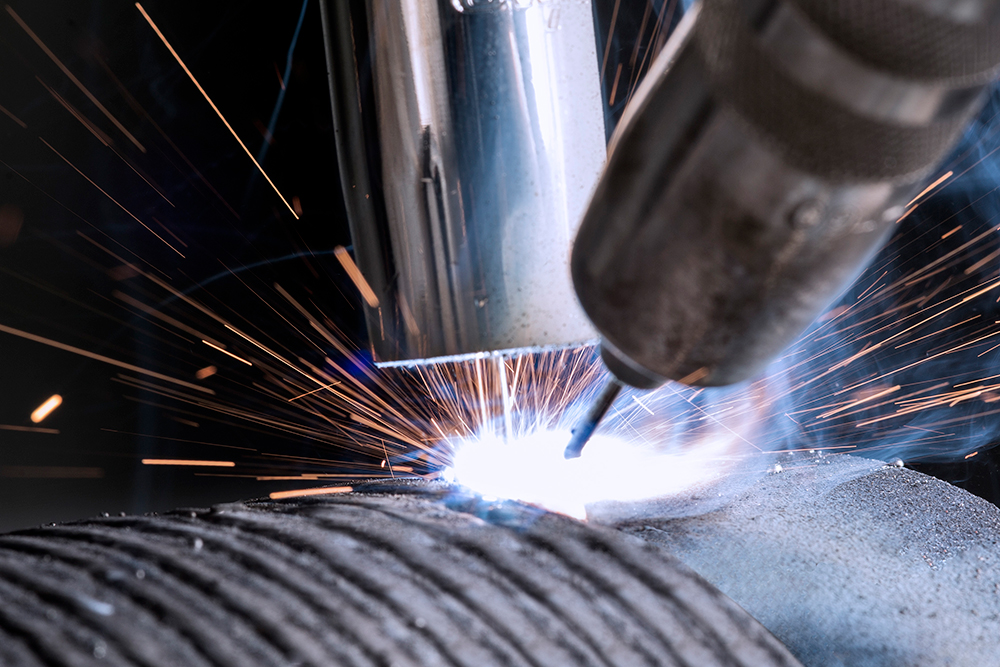
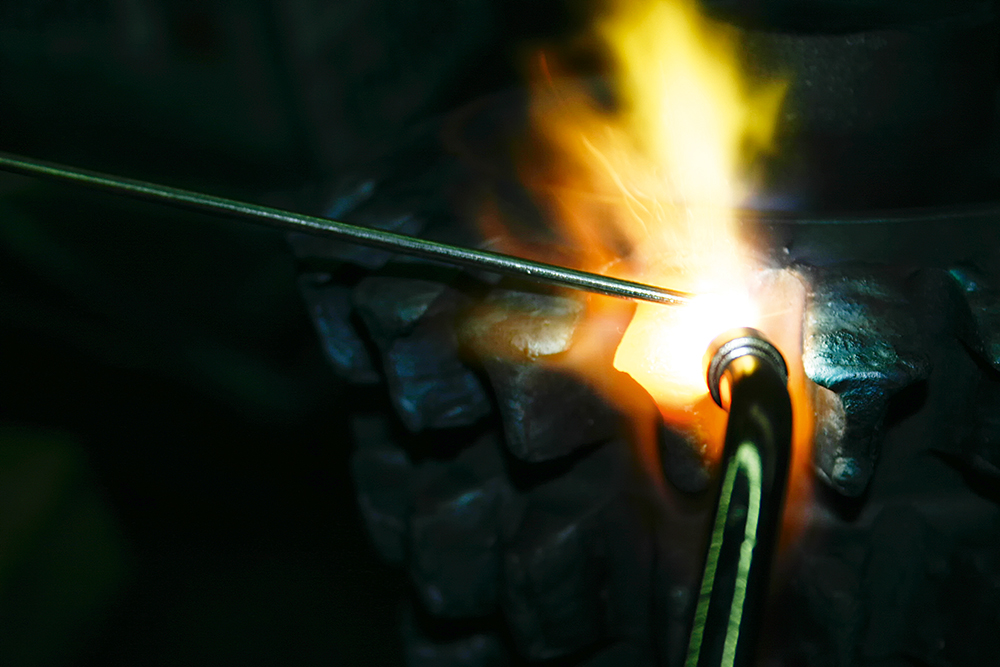
Callback service
Welding process
MIG/MAG/OA
At Metal inert gas welding (MSG) an arc burns between a consumable wire electrode, which is also a filler metal, and the workpiece. The arc is protected from the atmosphere by an inert gas bell. The inert shielding gases used are Argon (Ar), Helium (He) or mixtures of both gases are used. Since noble gases do not undergo chemical reactions even at very high temperatures, they represent a ideal protection for the melting bath.
Self-protecting Cored wires offer a special feature here, as they do not require the addition of inert gas. "Open Arc" (OA) can be welded. The reason for this lies in the powder filling of the wire, which, in addition to the alloying elements, also contains arc stabilizers and shielding gas formers.
The wire-shaped coating used for the hardfacing Welding filler metal is conveyed by a coil at a set, constant speed from the electrode feeder through the torch into the arc, where it melts and forms with the workpiece a substance-to-substance bond enters
The versatility of MIG welding
Plasma powder cladding (PTA)
The Plasma Powder Arc Welding (PPA), also called "Plasma Transferred-Arc (PTA)", is characterized by the use of the plasma beam with non-melting electrode as the primary heat source. In most cases, two arcs are used for buildup welding, which can be controlled independently of each other with separate current sources. The non-transmitting arc (pilot arc) burns between the plasma electrode and the plasma nozzle. It is started by a high-frequency (HF) ignition unit and forms the basis for the Ignition of the main arcwhich burns between the workpiece and the plasma electrode. By means of strong HF ignition units, however, the non-transmitting pilot arc can be dispensed with, as this would reduce the Arc can be ignited directly between the electrode and the workpiece.
The automated process of plasma powder cladding (PTA).
The plasma powder cladding (PTA) process can be easily automated so that a high degree of Reproducibility of the buildup weld layers is ensured. In addition, due to the locally highly concentrated heat source, very low degrees of mixing with the ferrous base material are achieved, which means that already in the first layer the required alloy characteristics be achieved. Likewise, a high utilization of the gas atomized powder used is realized, so that only very Low powder losses are produced during the welding process. The powder form of the welding filler material enables the application of numerous materials as well as various material combinations with a wide range of hardness values and other properties.
Oxyacetylene welding
Oxyacetylene welding is one of the oldest welding processes. This technique is used because of its high flexibility and Mobility widely used in industry and the trades. In oxyacetylene welding, a fuel gas is mixed with oxygen in a welding torch in such a way that a flame is produced which causes the base material to melt but does not oxidize it. Two different variants belong to oxyacetylene welding:
Gas powder buildup weldingIn this process, a powdered filler material is fed into the flame directly in the burner or from outside and is thus melted and the Deposition welding with welding rodIn this process, the filler metal is fed into the flame as a rod or wire.
Advantages of oxyacetylene welding
The gases used can be carried in cylinders or taken from stationary systems. Further advantages of this welding process are the Separate supply of Heat and filler metal and the resulting good suitability for Forced position welding as well as the good accessibility to confined welding areas. At the usually low welding speeds, only small welding residual stresses are usually induced and the hardening tendency as well as segregation is extremely low.
Manual arc welding (E-hand)
The Manual arc weldingalso known as "E-Hand", is one of the most flexible and easy to use systems available on the market. most commonly used welding methods. The welder guides the rod electrode clamped in an electrode holder in the direction of the molten pool. The current flow results from the fact that both the electrode holder and the workpiece are connected to the two different poles.
The arc is ignited by briefly placing the electrode on the workpiece and then lifting it off (contact ignition). The applied ignition voltage accelerates the electrons thermally emitted by the short circuit and thus enables a stable and permanent arcing by impact ionization of the discharge atmosphere.
The arc melts the electrode and simultaneously liquefies the base metal. The molten coating has arc stabilizers, shielding gas and slag formers to ensure a stable welding process. By tracking the electrode, the arc length is kept constant and, at the same time, the arc is moved in the working direction to achieve a continuous welding progress to achieve.
Laser powder cladding (LPA)
At Laser powder cladding (LPA) the laser melts the component surface local on. The filler metal is fed to the fusion spot in powder form using a powder nozzle. The movement of the process head with laser optics and powder nozzle produces weld beads on the component. Bead after bead, surfaces can be coated and layer after layer of coating thickness can be increased or reduced. whole geometries or restore them. But wear protection layers can also be generated in this way with wire-shaped welding filler materials.
Applications of the LPA
Due to its good focusability energy densities can be achieved with the laser that are very difficult to achieve with conventional thermal processes. This allows the processing of components with Minimal thermal stress and distortion. Laser cladding is therefore particularly suitable for components with high requirements in terms of tolerances. Other applications include difficult-to-weld nickel-based materials in gas turbines and tungsten carbide wear-resistant coatings. Typical components are turbine blades, drilling tools and pump parts.
Laser wire buildup welding (LDA)
At the process Laser wire buildup welding (LDA) the laser beam melts the wire and the base material, the melt bonds firmly and solidifies again until a small bump remains. When the individual welding paths overlap precisely, the desired shape is gradually applied.
Areas of application of laser buildup welding with wire are the Repair components as well as the Functionalizing surfaces. The process is particularly economical, clean and rework is reduced to a minimum.
Different welding wires are available as additional material. So it is possible, homogeneous material or to create functional layers according to the coating requirements.
Tungsten inert gas welding (TIG)
The Tungsten inert gas welding (TIG welding for short) was developed in the USA and was originally called "Argonarc welding". Other names by which it was introduced in Europe were "Arcatom welding" (standard designation tungsten-hydrogen welding) and "Heliarc". In English-speaking countries, it is called TIG welding (tungsten-inert gas welding) in the UK and GTAW (gas-tungsten arc welding) in the USA.
How does TIG welding
In TIG welding, a welding torch burns between the non-melting tungsten electrode and the workpiece the arc. The tungsten electrode sits in a torch through which inert shielding gas flows to protect the tungsten electrode, molten pool and melting welding filler metal from Oxidation by atmospheric oxygen. The rod-shaped filler metal is fed laterally into the arc and the molten pool, thus joining the two workpieces. TIG welding is used in all industries preferred where high quality seams are required, e.g. in aerospace, power plant construction, the food industry, apparatus and container engineering, and precision mechanics.
MSG Hot Wire Welding (MSG-HD)
The MSG hot wire buildup welding has its origins in the 1980s in the form of cold-wire assisted MSG buildup welding as well as submerged-arc welding, in which the decoupling of material and energy input with the aid of an external filler wire has already been set as a goal. The use of Cold wire has proven to be disadvantageous, however, because of the limited material input, which depends on the heat transfer of the arc and molten bath.
The invention of the Hot Wire Technology finally enables the wire temperature and thus deposition rate to be controlled largely independently of the arc and melt pool temperature, with the wire being preheated before entering the melt pool on the basis of ohmic resistance.
Hot wire feeding advantages
When feeding a hot wire, the aim is to achieve a heating of just under Below the melting temperatureAs a result, the amount of residual heat required to melt the filler wire is significantly lower compared with cold wire use. The main advantages of the MSG hot-wire buildup welding process is primarily the independent control of deposition rate and penetration depth, so that in buildup welding improved layer properties can be achieved already from the first layer due to reduced mixing with the base material.
PTA Hot Wire Welding (PTA-HD)
In PTA hot-wire welding (PTA-HD), the actual plasma powder buildup welding process is followed by a additional hot wire is added, which has several advantages: mixing with the base material can be reduced while at the same time increasing the deposition rate. Furthermore, no metallic reactions occur during the melting of the wire, so that the applied layers very pure are. A further advantage is offered by the use of an additional hot wire for the introduction of large carbide grains, e.g. tungsten seltzer carbide (WSC), which are limited in PTA welding to up to approx. 250 µm.
TIG hot wire welding (TIG-HD)
By using an additional welding wire, the range of applications for the automated TIG welding be significantly expanded. In the process, a distinction is made between the cold and hot wire variants. With the Cold wire feeder the filler metal is fed to the welding point without current and melted in the arc. This is suitable wherever a rapid welding speed, Gap bridging and Filling volume are required. In addition, TIG welding with cold wire is used when a special seam appearance and visual quality are to be achieved. It is suitable for all common types of wire.
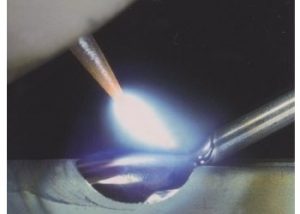
Hot wire welding process
At Hot Wire Welding the wire is heated to the melting point by an additional hot wire module. As a result, less heat is extracted from the arc and the weld pool. By preheating the wire, its deposition rate can be increased even further compared with cold wire welding. This results in a significant Increasing the welding speedwhich is similar to that of a MIG/MAG process, but splash- and emission-free is. In addition to joint welding, the hot wire process is also ideally suited for buildup welding, as it involves less melting of the base material.