With DURMAT® achieve improved, higher-performance wear alloys
The high demands made today on the wear resistance of alloys based on Tungsten carbide and Cobalt are leading to ever finer microstructures with optimized compositions. This results in improved, higher-performance wear alloys.
DURMAT® | Chem. Composition | Hardness | Applications | Features |
---|---|---|---|---|
WSC | WC-W2C | 2.360HV0.1 | Deep drilling tools, drill pipes, crushers, mixers, concrete and stone saws, transport screws, extruder housings | Armoring of surfaces subject to extremely high mechanical stresses consisting of abrasion and friction |
SWSC | WC-W2C | 3.000HV0.1 | Deep drilling tools, drill pipes, crushers, mixers, concrete and stone saws, transport screws, extruder housings | Armoring of surfaces subject to extremely high mechanical stresses consisting of abrasion and friction |
RF 13 | WC-Co 94/6 | 1.950-2.050HV0.1 | Rock bits, special tools for deep drilling | WC Co alloy with fine WC Very good abrasion and corrosion resistance |
MCWC | Monocrystalline tungsten carbide with 6.12 % C content | 1.600HV0.1 | PTA coatings on wear parts | Good wear resistance Good thermal stability Less hardness than WSC/SWSC |
WC IV | Broken tungsten carbide with 6-10 % Co content | 1.500-1.800HV0.1 | Mining, deep drilling technology, tool joints in the oil industry | High wear resistance Especially suitable for cutting tool |
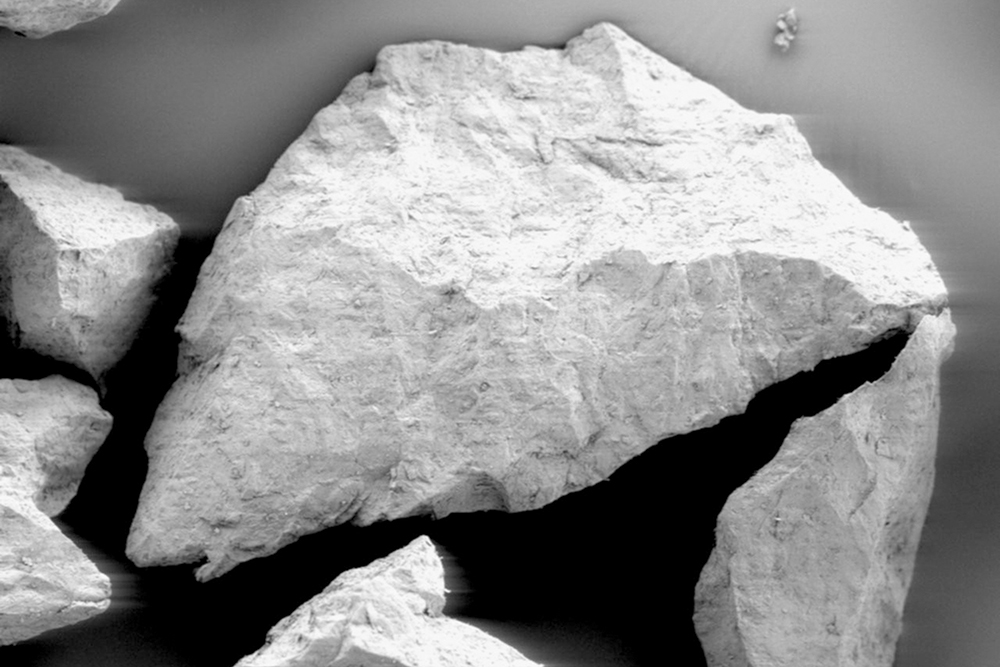
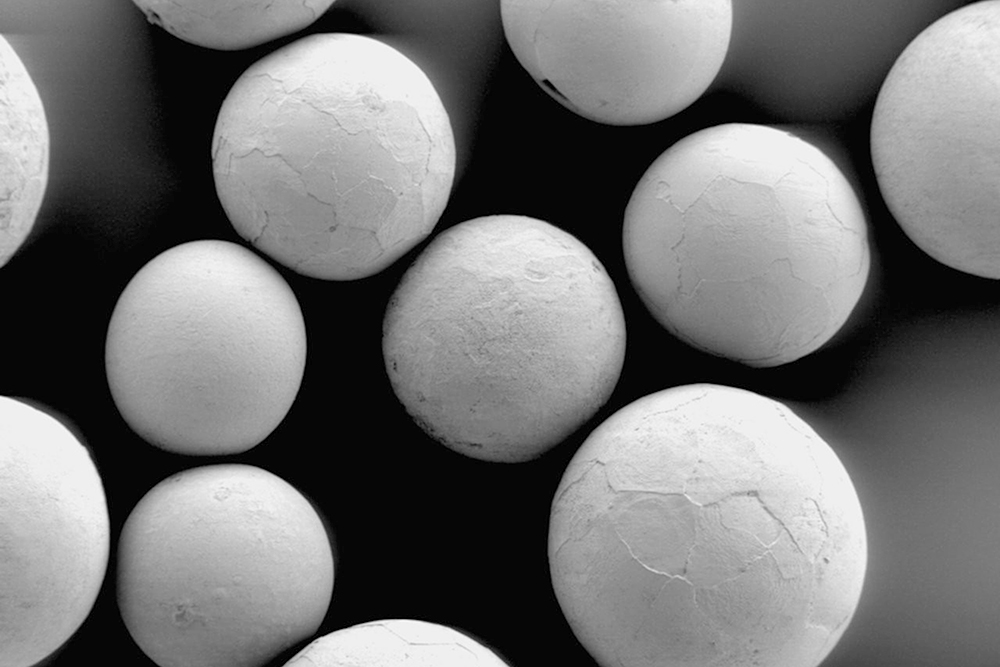
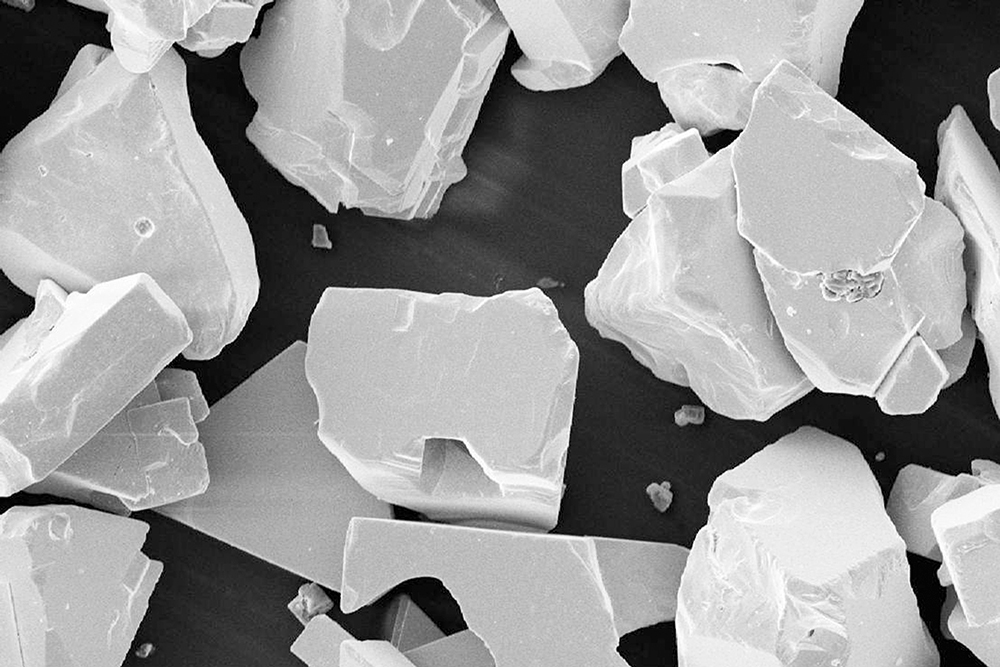
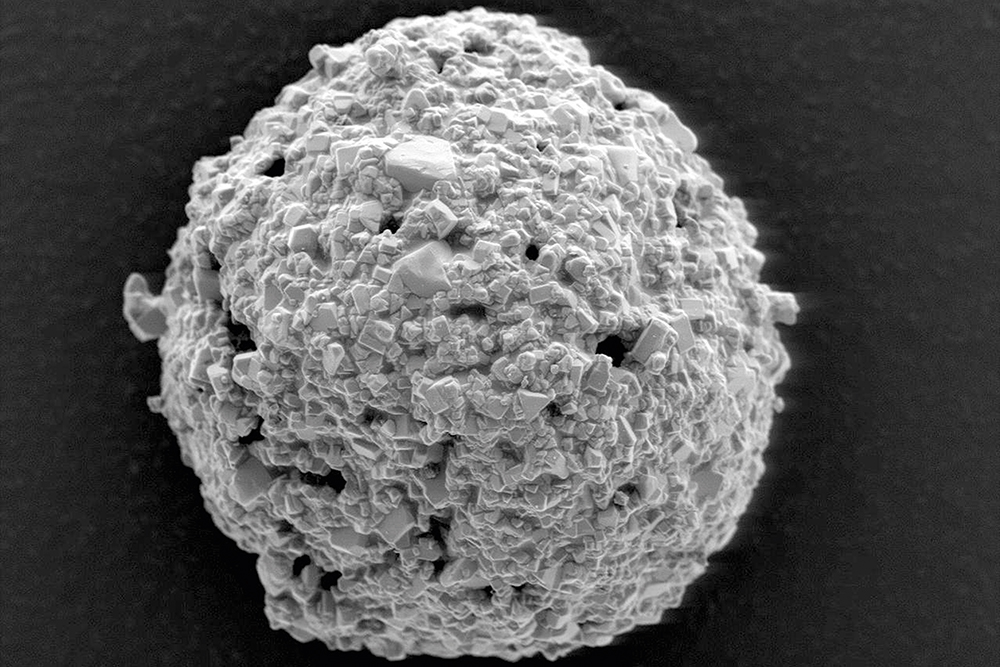
- Request information material
Notice: The mandatory field is marked. All other fields are voluntary. Your data will only be collected and stored electronically strictly for the purpose of processing and responding to your request. Information on data processing can be found here: Privacy.